Specialist Tips for Picking the Right Metal Stamping Services for Your Demands
Specialist Tips for Picking the Right Metal Stamping Services for Your Demands
Blog Article
Checking Out the Globe of Metal Stamping: From Layout to Manufacturing
Within the world of manufacturing, steel marking sticks out as a specific and reliable method for forming metal sheets into various kinds with amazing consistency. From the initial design phase where complex patterns materialize to the elaborate production processes, steel stamping is a mix of virtuosity and engineering. Exploring this globe unveils a complex interaction of imagination and technical proficiency, using a look into a realm where advancement fulfills craftsmanship.
History of Steel Stamping
Metal stamping, a widely utilized production process today, has an abundant history that goes back to old times (Metal Stamping). The beginnings of steel stamping can be mapped to ancient human beings such as the Egyptians, who utilized marking methods to decorate jewelry and accessories with complex designs. In time, metal stamping progressed, with human beings like the Greeks and Romans using it for developing coins and ornamental products
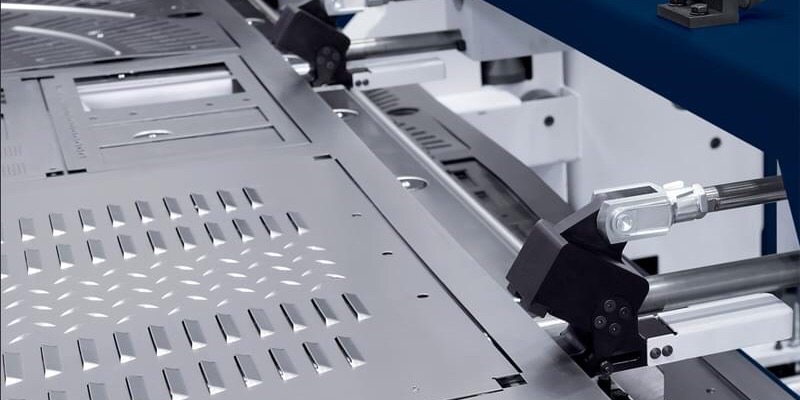
In the 20th century, steel marking remained to progress with the integration of automation and computer system mathematical control (CNC) innovation. These improvements further enhanced the performance and accuracy of metal marking procedures, making it a crucial component of contemporary manufacturing throughout markets such as auto, aerospace, and electronics. Today, steel stamping continues to be an essential manufacturing process, combining practice with advancement to satisfy the needs of a continuously evolving sector.
Layout Considerations and Prototyping
When establishing metal marking jobs, meticulous focus to create factors to consider and prototyping is necessary for making sure optimum manufacturing results. Style factors to consider in steel stamping include product choice, component geometry, tooling layout, and production usefulness. Choosing the best product is critical as it influences the part's performance, expense, and manufacturability. Component geometry affects the intricacy of the stamping procedure and the performance of the last product. Tooling style plays a considerable role in the success of steel stamping tasks, affecting part accuracy, device long life, and production effectiveness.
Prototyping is an important phase in the metal marking procedure that enables designers to evaluate the design, verify manufacturability, and make needed adjustments before full-blown production. Prototyping aids recognize possible concerns at an early stage, conserving time and costs in the long run. It also provides a possibility to enhance the design for effectiveness and high quality. By carefully considering design facets and making use of prototyping, producers can streamline the metal stamping process and accomplish high-quality, cost-effective manufacturing end results.
Tooling and Tools Fundamentals
Thinking about the critical role that tooling design plays in the success of steel marking jobs, comprehending the necessary devices and devices called for is critical for achieving efficient production results. Fixtures hold the steel in place during the marking process, ensuring accuracy and repeatability. Investing in top notch tooling and equipment not only why not try these out enhances production performance yet also leads to higher precision, minimized waste, and total price savings in metal marking procedures.
Production Refine and Quality Assurance
Successfully taking care of the manufacturing process and applying robust high quality control procedures are important for ensuring the success of steel marking tasks. The production procedure in metal stamping involves a collection of actions that must be carefully worked with to achieve ideal outcomes.
Quality control in steel stamping is extremely important to provide products that satisfy the called for specifications. By keeping stringent top quality control criteria, manufacturers can copyright their track record for supplying high-quality metal stamped products.
Applications and Market Insights
In the world of steel stamping, the effective application of manufacturing procedures and quality control steps directly influences the efficiency and reliability of different sector applications and provides beneficial insights right into the field's functional characteristics. Metal stamping locates widespread application throughout diverse industries, consisting of automotive, aerospace, electronics, and appliances. In the automotive market, metal marking plays an essential function in generating components such as chassis, braces, and architectural components with high accuracy and efficiency. The aerospace view it now industry counts on metal marking for making intricate components like panels, braces, and fittings that satisfy rigorous quality standards (Metal Stamping). In the electronics market, metal stamping is utilized to produce exact parts like connectors, terminals, and heat sinks. Additionally, metal stamping assists in the manufacturing of different family appliances, consisting of fridges, washing makers, and ovens, by offering cost-effective options for producing long lasting and intricate components. Understanding the applications and sector insights of metal stamping is crucial for optimizing production procedures and improving product high quality across various markets. advice
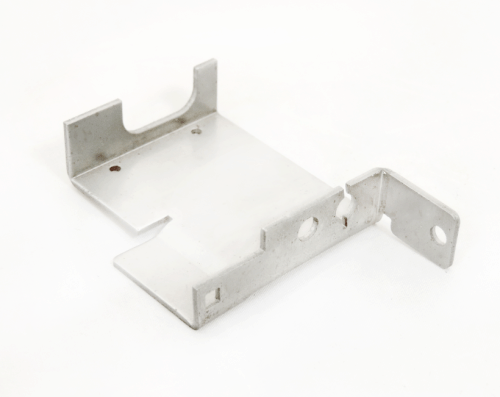
Conclusion
Style factors to consider, prototyping, tooling, devices, manufacturing processes, and high quality control are necessary elements of metal stamping. With its prevalent applications and sector understandings, metal marking continues to be a functional and efficient manufacturing procedure.
Report this page